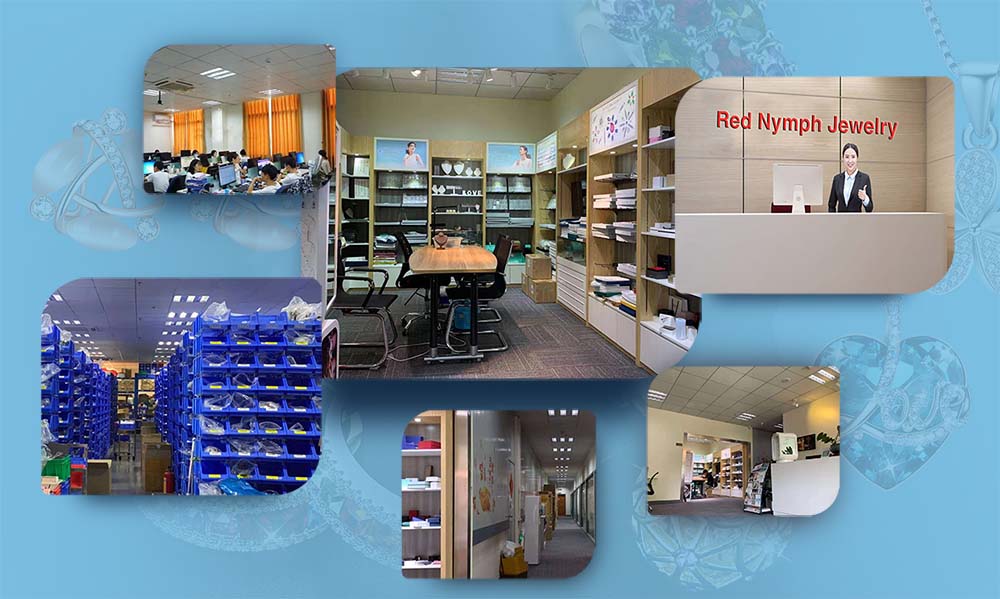
Pink Nymph Jewellery
One thing exceptional occurred to jewellery design and manufacturing previously few years – it underwent a technological revolution powered by Laptop-Aided Design (CAD) software program and Laptop-Aided Manufacturing (CAM) {hardware}, akin to 3D printers.
Earlier than these technological advances, designers started by sketching a bit of bijou, and when it was finalized, they used pencil, pen, or watercolor paint to create a rendering of the design . Jewelers then used the drawing to both hand-fabricate the piece out of steel or carve it out of wax. The wax mannequin was encased in plaster and positioned in an oven. As soon as the wax was burned away, molten treasured steel, like gold or platinum, was poured into the cavity left by the wax . After it cooled, the plaster was damaged aside and the piece of bijou was completed.
Designers nonetheless use most of the steps on this course of, particularly when making high-end items. And regardless of all the brand new CAD and CAM expertise, jewellery designers nonetheless have to have good engineering abilities – like figuring out how robust prongs need to be to carry a gemstone in place .
Nonetheless, expertise has basically modified how jewellery is designed and manufactured.
Laptop-Aided Design
A lot of immediately’s jewellery is now designed utilizing CAD software program. The attract is comprehensible: CAD permits designers to work extra rapidly, simply create variations of a design theme, and “minimize and paste” motifs into totally different tasks extra rapidly than if drawn by hand. Designers also can save favourite purposeful or ornamental components in a library and use them in future items.
The extra advanced a bit of bijou is, the tougher it’s to design . One other approach that CAD software program is altering design is that it permits designers to zoom in to allow them to add element to very small areas of a bit.
CAD additionally helps the artistic course of. A superb design is normally the results of appreciable experimentation. CAD makes trial and error simple (you possibly can’t rapidly “undo” one thing you don’t like in a watercolor). Designers can comply with their creativeness with out having to recreate the design every time they’re impressed.
CAD additionally lets designers create photorealistic photographs of bijou which have shadows and reflections. These computer-generated photographs are so lifelike they’ll even idiot an knowledgeable’s eyes. These photographs let customers and inventive administrators get a very good sense of what a completed piece will seem like earlier than it’s made.
Laptop-Aided Manufacturing and 3D Printers
Previously, producers used rubber molds to make duplicates of the unique grasp mannequin. Nonetheless, if variations on that mannequin have been wanted, the mannequin maker must create an entire new mannequin. With CAD software program, adjustments can made with clicks of a mouse, and the brand new mannequin may be printed on demand on a CAM machine, akin to a 3D printer. 3D printers allow producers to print resin prototypes of the CAD mannequin that may be simply solid.
Laser Sintering
Laser sintering guarantees to be the subsequent huge factor to revolutionize jewellery manufacturing. A laser melts powdered steel, like gold, platinum, or silver, layer by layer into the form of a bit. Items with working hinges and pins may be made – no small feat. The expertise continues to be fairly costly and in its infancy, however it might remove the necessity to create a wax or plastic mannequin of a bit after which solid it. In different phrases, a designer might go from a CAD mannequin to a completed piece with just some mouse clicks.
Trying Again to Look Forward
Ten years in the past, the notion of designing a bit of bijou on a pc appeared farfetched to some. Ten years from now, designers could create a bit in CAD, ship it to a laser sintering machine, and maintain a near-completed work of their arms. What’s extra, each bit might be personalized to the patron’s specs. It’s undoubtedly an thrilling time to be a designer and a jewellery connoisseur.